Mouthguard Impact Force Testing System
Mouthguard Impact Force Testing System
Mouthguard Impact Force Testing System
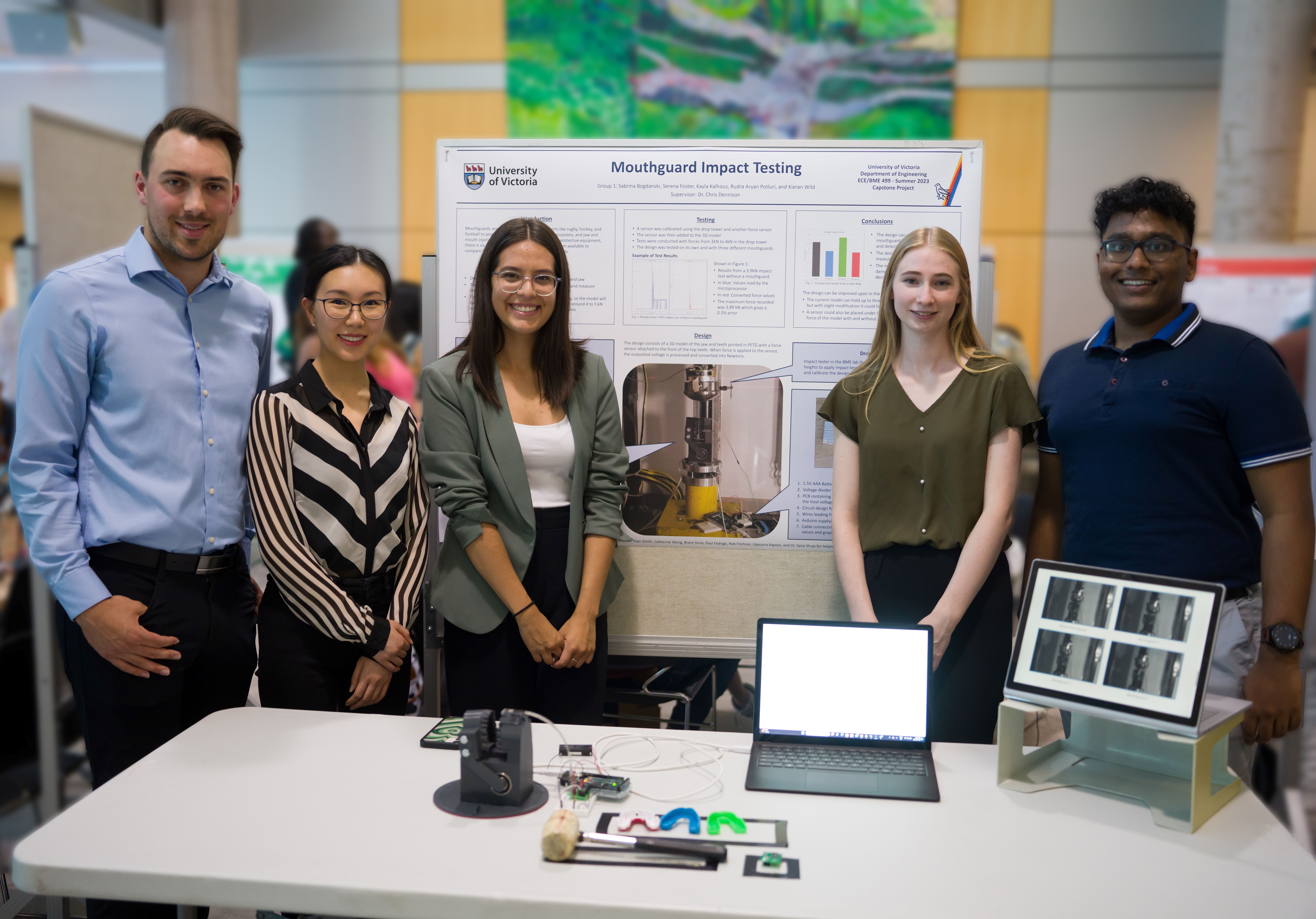
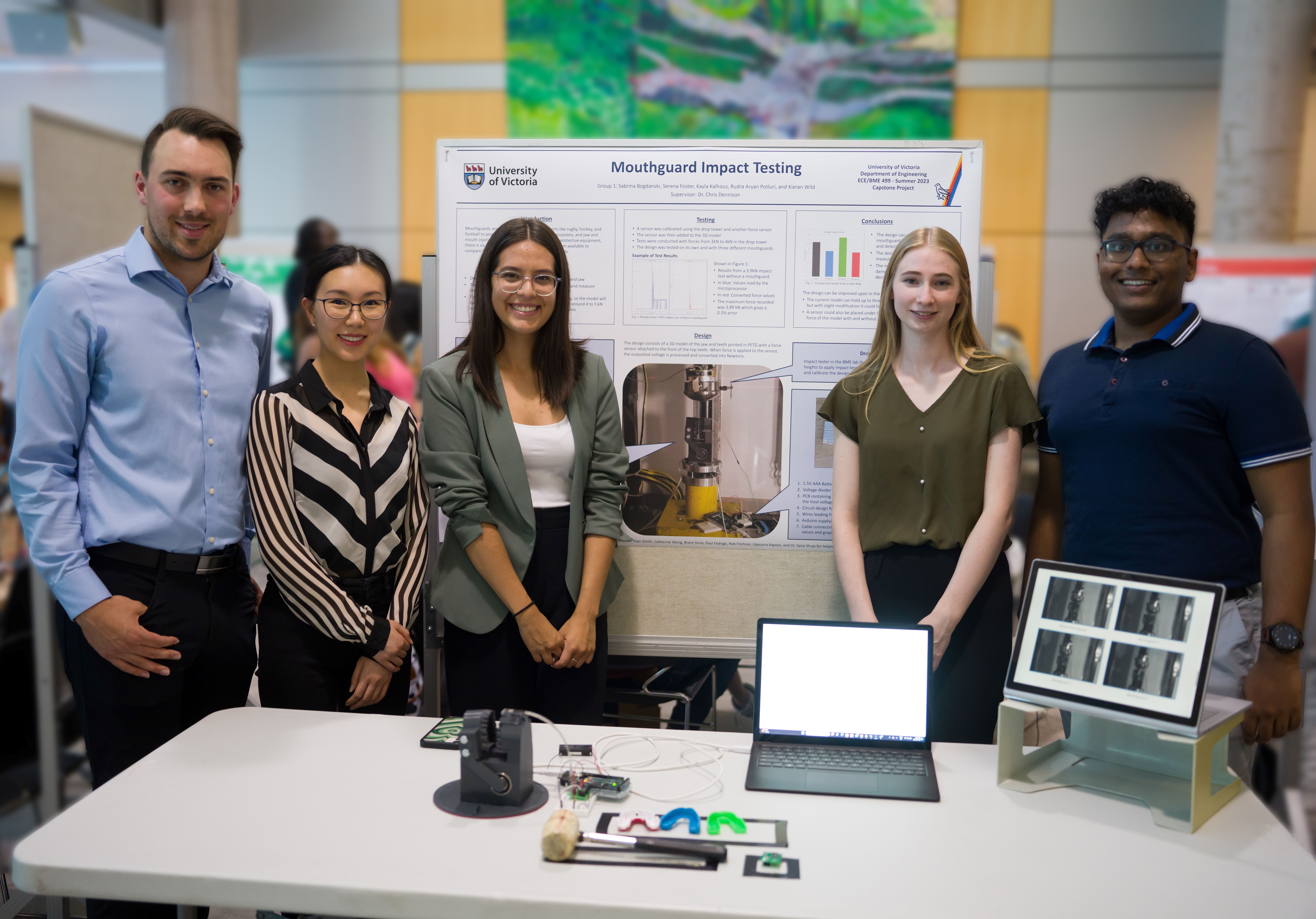
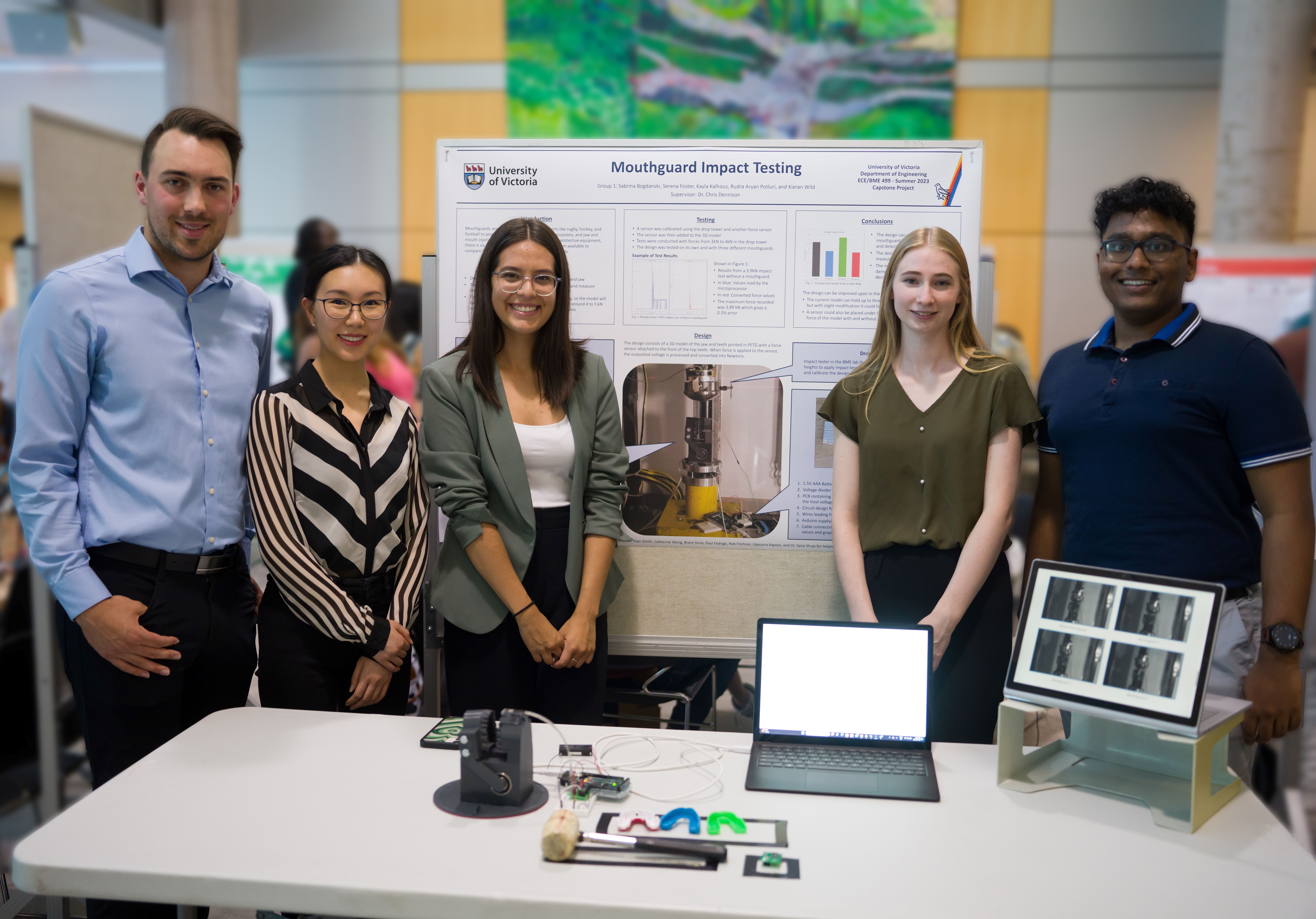
Overview
For our BME/ECE 499 capstone project, my team and I developed a testing system to measure impact forces on sports mouthguards, specifically for rugby applications. This project aimed to create a standardized method for evaluating the effectiveness of mouthguards in reducing impact forces, thus improving player safety.
Technical Approach
System Components:
Jaw Model: A 3D printed human jaw model with integrated sensors.
Sensors: Tekscan force sensors to measure impact forces on the teeth.
Data Acquisition System: Arduino microcontroller for data logging and sensor interfacing.
Drop Tower: Used to apply controlled impact forces to the jaw model.
Software: Python application for data visualization and analysis.
Development Process:
Background and Planning: We began by researching existing methods for measuring impact forces on mouthguards. We identified the need for a reliable, repeatable testing system that could be used to develop a safety rating for mouthguards.
Jaw Model Design and Fabrication: The jaw model was designed using CAD software and 3D printed using durable materials to withstand repeated impacts.
Sensor Integration: Tekscan force sensors were integrated into the model to measure impact forces directly on the teeth.
Data Acquisition System: An Arduino microcontroller was used to interface with the sensors and log data during impact tests.
Impact Testing Setup: A drop tower was constructed to apply controlled impacts to the jaw model. The height and weight of the drop assembly were chosen to simulate typical forces experienced in rugby.
Software Development: A Python application was developed to visualize and analyze the data collected during impact tests. The application included a user interface to start and stop tests, display real-time force measurements, and log data for further analysis.
Challenges and Solutions
Sensor Calibration:
Challenge: Ensuring accurate force measurements from the sensors.
Solution: We calibrated the sensors using a known force transducer and a drop tower setup. Calibration curves were generated to convert sensor readings to force values.
Data Logging and Analysis:
Challenge: Developing a reliable system for logging and analyzing impact data.
Solution: The Arduino microcontroller was programmed to log sensor data during impacts. The Python application provided real-time visualization and stored data for post-test analysis.
Impact Simulation:
Challenge: Accurately simulating the forces experienced during rugby impacts.
Solution: The drop tower was designed to apply consistent and repeatable impacts. Various heights and weights were tested to ensure a range of impact forces were covered.
Project Outcomes
Current Functionality:
The testing system accurately measures impact forces on mouthguards using integrated sensors.
Data is logged and visualized in real-time, providing immediate feedback on the effectiveness of the mouthguard.
The system can simulate a range of impact forces, making it suitable for evaluating different mouthguard designs.
Performance Metrics:
The system successfully measured forces up to 4.5 kN, meeting the project’s design objectives.
The 3D printed jaw model withstood repeated impacts without damage, demonstrating its durability.
Limitations:
The current setup does not measure bite force, which could provide additional insights into mouthguard performance.
Sensors were placed on limited teeth due to project constraints, which may not capture all impact dynamics.
Future Improvements
Extended Sensor Coverage: Integrating sensors on additional teeth to capture a more comprehensive impact profile.
Bite Force Measurement: Adding sensors to measure bite force, providing further data on mouthguard effectiveness.
Advanced Data Analysis: Implementing machine learning algorithms to analyze impact data and predict injury risk.
Conclusion
The Mouthguard Impact Force Testing System project successfully developed a reliable and repeatable method for evaluating the effectiveness of sports mouthguards. By integrating sensors into a 3D printed jaw model and using a controlled impact testing setup, we provided valuable insights into the performance of mouthguards, contributing to player safety in contact sports.
Overview
For our BME/ECE 499 capstone project, my team and I developed a testing system to measure impact forces on sports mouthguards, specifically for rugby applications. This project aimed to create a standardized method for evaluating the effectiveness of mouthguards in reducing impact forces, thus improving player safety.
Technical Approach
System Components:
Jaw Model: A 3D printed human jaw model with integrated sensors.
Sensors: Tekscan force sensors to measure impact forces on the teeth.
Data Acquisition System: Arduino microcontroller for data logging and sensor interfacing.
Drop Tower: Used to apply controlled impact forces to the jaw model.
Software: Python application for data visualization and analysis.
Development Process:
Background and Planning: We began by researching existing methods for measuring impact forces on mouthguards. We identified the need for a reliable, repeatable testing system that could be used to develop a safety rating for mouthguards.
Jaw Model Design and Fabrication: The jaw model was designed using CAD software and 3D printed using durable materials to withstand repeated impacts.
Sensor Integration: Tekscan force sensors were integrated into the model to measure impact forces directly on the teeth.
Data Acquisition System: An Arduino microcontroller was used to interface with the sensors and log data during impact tests.
Impact Testing Setup: A drop tower was constructed to apply controlled impacts to the jaw model. The height and weight of the drop assembly were chosen to simulate typical forces experienced in rugby.
Software Development: A Python application was developed to visualize and analyze the data collected during impact tests. The application included a user interface to start and stop tests, display real-time force measurements, and log data for further analysis.
Challenges and Solutions
Sensor Calibration:
Challenge: Ensuring accurate force measurements from the sensors.
Solution: We calibrated the sensors using a known force transducer and a drop tower setup. Calibration curves were generated to convert sensor readings to force values.
Data Logging and Analysis:
Challenge: Developing a reliable system for logging and analyzing impact data.
Solution: The Arduino microcontroller was programmed to log sensor data during impacts. The Python application provided real-time visualization and stored data for post-test analysis.
Impact Simulation:
Challenge: Accurately simulating the forces experienced during rugby impacts.
Solution: The drop tower was designed to apply consistent and repeatable impacts. Various heights and weights were tested to ensure a range of impact forces were covered.
Project Outcomes
Current Functionality:
The testing system accurately measures impact forces on mouthguards using integrated sensors.
Data is logged and visualized in real-time, providing immediate feedback on the effectiveness of the mouthguard.
The system can simulate a range of impact forces, making it suitable for evaluating different mouthguard designs.
Performance Metrics:
The system successfully measured forces up to 4.5 kN, meeting the project’s design objectives.
The 3D printed jaw model withstood repeated impacts without damage, demonstrating its durability.
Limitations:
The current setup does not measure bite force, which could provide additional insights into mouthguard performance.
Sensors were placed on limited teeth due to project constraints, which may not capture all impact dynamics.
Future Improvements
Extended Sensor Coverage: Integrating sensors on additional teeth to capture a more comprehensive impact profile.
Bite Force Measurement: Adding sensors to measure bite force, providing further data on mouthguard effectiveness.
Advanced Data Analysis: Implementing machine learning algorithms to analyze impact data and predict injury risk.
Conclusion
The Mouthguard Impact Force Testing System project successfully developed a reliable and repeatable method for evaluating the effectiveness of sports mouthguards. By integrating sensors into a 3D printed jaw model and using a controlled impact testing setup, we provided valuable insights into the performance of mouthguards, contributing to player safety in contact sports.
Overview
For our BME/ECE 499 capstone project, my team and I developed a testing system to measure impact forces on sports mouthguards, specifically for rugby applications. This project aimed to create a standardized method for evaluating the effectiveness of mouthguards in reducing impact forces, thus improving player safety.
Technical Approach
System Components:
Jaw Model: A 3D printed human jaw model with integrated sensors.
Sensors: Tekscan force sensors to measure impact forces on the teeth.
Data Acquisition System: Arduino microcontroller for data logging and sensor interfacing.
Drop Tower: Used to apply controlled impact forces to the jaw model.
Software: Python application for data visualization and analysis.
Development Process:
Background and Planning: We began by researching existing methods for measuring impact forces on mouthguards. We identified the need for a reliable, repeatable testing system that could be used to develop a safety rating for mouthguards.
Jaw Model Design and Fabrication: The jaw model was designed using CAD software and 3D printed using durable materials to withstand repeated impacts.
Sensor Integration: Tekscan force sensors were integrated into the model to measure impact forces directly on the teeth.
Data Acquisition System: An Arduino microcontroller was used to interface with the sensors and log data during impact tests.
Impact Testing Setup: A drop tower was constructed to apply controlled impacts to the jaw model. The height and weight of the drop assembly were chosen to simulate typical forces experienced in rugby.
Software Development: A Python application was developed to visualize and analyze the data collected during impact tests. The application included a user interface to start and stop tests, display real-time force measurements, and log data for further analysis.
Challenges and Solutions
Sensor Calibration:
Challenge: Ensuring accurate force measurements from the sensors.
Solution: We calibrated the sensors using a known force transducer and a drop tower setup. Calibration curves were generated to convert sensor readings to force values.
Data Logging and Analysis:
Challenge: Developing a reliable system for logging and analyzing impact data.
Solution: The Arduino microcontroller was programmed to log sensor data during impacts. The Python application provided real-time visualization and stored data for post-test analysis.
Impact Simulation:
Challenge: Accurately simulating the forces experienced during rugby impacts.
Solution: The drop tower was designed to apply consistent and repeatable impacts. Various heights and weights were tested to ensure a range of impact forces were covered.
Project Outcomes
Current Functionality:
The testing system accurately measures impact forces on mouthguards using integrated sensors.
Data is logged and visualized in real-time, providing immediate feedback on the effectiveness of the mouthguard.
The system can simulate a range of impact forces, making it suitable for evaluating different mouthguard designs.
Performance Metrics:
The system successfully measured forces up to 4.5 kN, meeting the project’s design objectives.
The 3D printed jaw model withstood repeated impacts without damage, demonstrating its durability.
Limitations:
The current setup does not measure bite force, which could provide additional insights into mouthguard performance.
Sensors were placed on limited teeth due to project constraints, which may not capture all impact dynamics.
Future Improvements
Extended Sensor Coverage: Integrating sensors on additional teeth to capture a more comprehensive impact profile.
Bite Force Measurement: Adding sensors to measure bite force, providing further data on mouthguard effectiveness.
Advanced Data Analysis: Implementing machine learning algorithms to analyze impact data and predict injury risk.
Conclusion
The Mouthguard Impact Force Testing System project successfully developed a reliable and repeatable method for evaluating the effectiveness of sports mouthguards. By integrating sensors into a 3D printed jaw model and using a controlled impact testing setup, we provided valuable insights into the performance of mouthguards, contributing to player safety in contact sports.